Maintenance and Care of CNC Cutting Machines: Key Steps to Extend Equipment Lifespan
- Company News
- -September 27, 2024
- - byKevin
- Home
- >
- News
- >
- Company News
- >
- Maintenance and Care of CNC Cutting Machines: Key Steps to Extend Equipment Lifespan
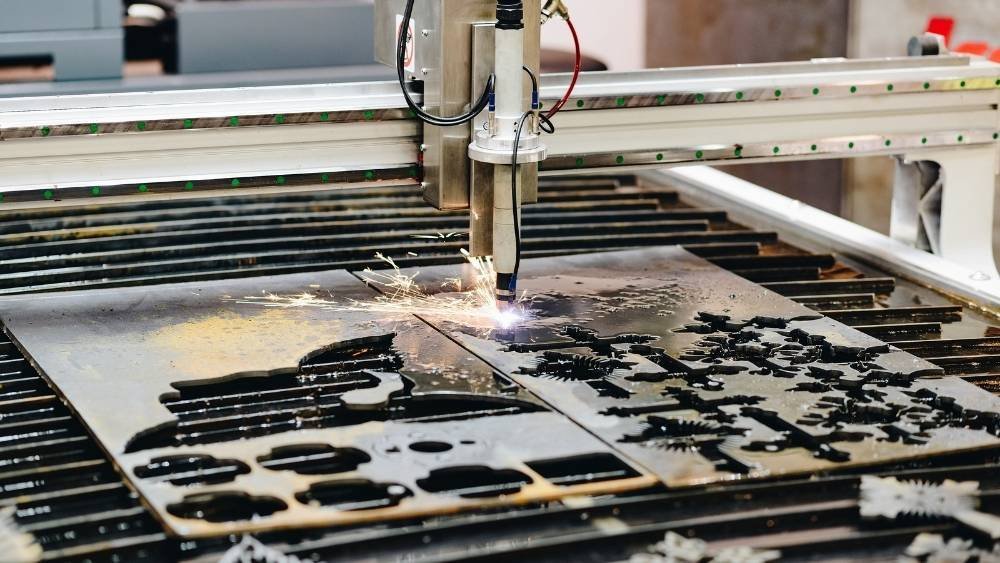
Table of Contents
CNC (Computer Numerical Control) cutting machines are pivotal in many industries, offering precision and efficiency in cutting materials like metal, wood, plastic, and more. However, these machines are significant investments, and proper maintenance is crucial to ensure they continue to perform optimally and have a long operational lifespan. In this blog, we will discuss the key steps to maintain and care for CNC cutting machines, ensuring their longevity and consistent performance.
1. Regular Cleaning and Inspection
One of the most basic yet vital maintenance tasks for CNC cutting machines is regular cleaning. Over time, dust, debris, and remnants from cutting operations can accumulate on the machine, leading to potential malfunctions or decreased efficiency. Here’s what you should focus on:
- Daily Cleaning: After each operation, remove any debris, especially from the cutting area and tool holders. Use compressed air to blow out dust from hard-to-reach areas, but ensure it’s done carefully to avoid forcing debris into sensitive components.
- Weekly Deep Cleaning: At least once a week, conduct a more thorough cleaning. Wipe down all surfaces, lubricate moving parts, and inspect the machine for signs of wear or damage.
- Routine Inspections: Regularly inspect the machine for loose screws, worn belts, or any signs of mechanical stress. Early detection of issues can prevent costly breakdowns.
2. Proper Lubrication
Lubrication is essential for the smooth operation of CNC machines. It reduces friction between moving parts, prevents wear, and helps in dissipating heat. Here’s how to manage lubrication effectively:
- Follow Manufacturer’s Guidelines: Always use the type of lubricant recommended by the machine’s manufacturer. Different parts of the machine may require different types of lubrication.
- Scheduled Lubrication: Establish a lubrication schedule based on the machine’s usage. High-use machines may require more frequent lubrication.
- Automated Lubrication Systems: Some CNC machines come with automated lubrication systems. Ensure these systems are functioning correctly and refill the lubricant reservoirs as needed.
3. Check and Replace Filters
CNC machines often have filters to keep the internal components clean and free from dust and debris. Over time, these filters can become clogged, reducing their effectiveness and potentially leading to overheating or mechanical failure.
- Regular Filter Checks: Inspect filters regularly, especially in environments with high levels of airborne particles. Replace or clean them as necessary.
- Cooling Systems Maintenance: The coolant system, if present, also needs attention. Ensure the coolant is clean and topped up to the appropriate level, and replace it as per the manufacturer’s guidelines.
4. Calibrate and Test Accuracy
The precision of a CNC cutting machine is one of its most critical features. Over time, wear and tear can lead to slight inaccuracies, which can compromise the quality of work. Regular calibration is essential to maintain accuracy:
- Monthly Calibration: At least once a month, perform a full calibration of the machine. This includes checking the alignment of the cutting tools, spindle, and table.
- Test Cuts: Periodically perform test cuts to check for accuracy. Compare the results against expected measurements and adjust the machine as needed.
- Tool Wear Monitoring: Tools that are worn out or damaged can lead to inaccuracies. Monitor tool condition regularly and replace them when necessary.
5. Monitor Software and Firmware Updates
CNC machines rely on sophisticated software and firmware to operate correctly. Keeping this software up-to-date is crucial for ensuring the machine runs efficiently and safely:
- Regular Updates: Check for updates from the machine manufacturer regularly. These updates can include bug fixes, performance improvements, and new features.
- Backup Configurations: Before applying any updates, ensure you have a backup of your current machine settings and configurations. This way, you can restore the machine to its previous state if something goes wrong during the update.
6. Maintain Electrical Components
The electrical components of a CNC machine are just as critical as the mechanical parts. Regular maintenance of these components ensures the machine runs smoothly and reduces the risk of electrical failures:
- Inspect Wiring and Connections: Regularly check for loose or frayed wires, as these can lead to shorts or other electrical issues.
- Check Power Supply: Ensure the machine is connected to a stable power supply. Fluctuations in voltage can damage sensitive electronic components.
- Clean Electrical Panels: Dust and debris can accumulate in electrical panels, leading to overheating or short circuits. Clean these areas carefully, ensuring power is disconnected before opening any panels.
7. Document and Track Maintenance Activities
Keeping detailed records of all maintenance activities is vital for several reasons. It helps in tracking the machine’s condition over time, identifying recurring issues, and ensuring all maintenance tasks are performed on schedule:
- Maintenance Log: Maintain a log that records every maintenance activity, including the date, type of maintenance, parts replaced, and any issues found.
- Scheduled Maintenance Reminders: Use software tools or a simple calendar system to set reminders for upcoming maintenance tasks. This ensures that nothing is overlooked.
- Operator Training: Ensure that all operators are trained to perform basic maintenance tasks and are familiar with the maintenance log.
8. Environmental Control
The environment in which a CNC machine operates can significantly affect its longevity and performance. Proper control of temperature, humidity, and cleanliness is essential:
- Temperature Control: Keep the machine in a temperature-controlled environment. Extreme temperatures can cause components to expand or contract, leading to misalignment or other issues.
- Humidity Control: Excessive humidity can lead to rusting of metal components, while too little humidity can cause static buildup, which might affect sensitive electronics.
- Clean Environment: Ensure the area around the machine is kept clean. Dust and debris can easily find their way into the machine, leading to potential problems.
9. Professional Maintenance and Servicing
While regular in-house maintenance is essential, professional servicing is also necessary to ensure the machine operates at its best:
- Annual Servicing: Have the machine professionally serviced at least once a year. This should include a comprehensive inspection, deep cleaning, and any necessary adjustments or repairs.
- Warranty and Support: Take advantage of the machine’s warranty and manufacturer support services. If you encounter an issue that you cannot resolve in-house, contact the manufacturer or a certified technician.
Conclusion
The longevity and performance of a CNC cutting machine are directly tied to how well it is maintained. Regular cleaning, proper lubrication, routine inspections, and timely calibration are just a few of the essential steps in ensuring your machine remains in top condition. By following the key maintenance steps outlined in this blog, you can extend the lifespan of your CNC cutting machine, reduce downtime, and ensure it continues to produce high-quality results for years to come.
Investing time in regular maintenance not only protects your investment but also contributes to the overall efficiency and productivity of your operations. Keep your CNC machine in top shape, and it will reward you with consistent, precise, and reliable performance.
Post Categories
Post Tags
Product Categories
About Company
Related Posts
Application Areas for Industrial Chillers
Industrial chillers are crucial for maintaining optimal conditions in various industrial processes. By removing excess heat from equipment or materials,
The Science of Choosing Sunscreen: Protection Strategies for Different Skin Types
Sunscreen is designed to protect the skin from the harmful effects of ultraviolet (UV) radiation, which comes from the sun.
A Buyer’s Guide to Pet Food: How to Choose the Right Food for Your Pet
Before diving into the types of pet food available, it’s important to understand the basic nutritional needs of your pet.
A Buyer’s Guide to High-Efficiency Automated Packaging Machines: Secrets to Boosting Production Efficiency
Automated packaging machines are sophisticated systems designed to automate various aspects of the packaging process. From filling and sealing to
Submit to get the latest updates
Simply enter your email below and click "Submit" to stay connected with everything new and exciting.